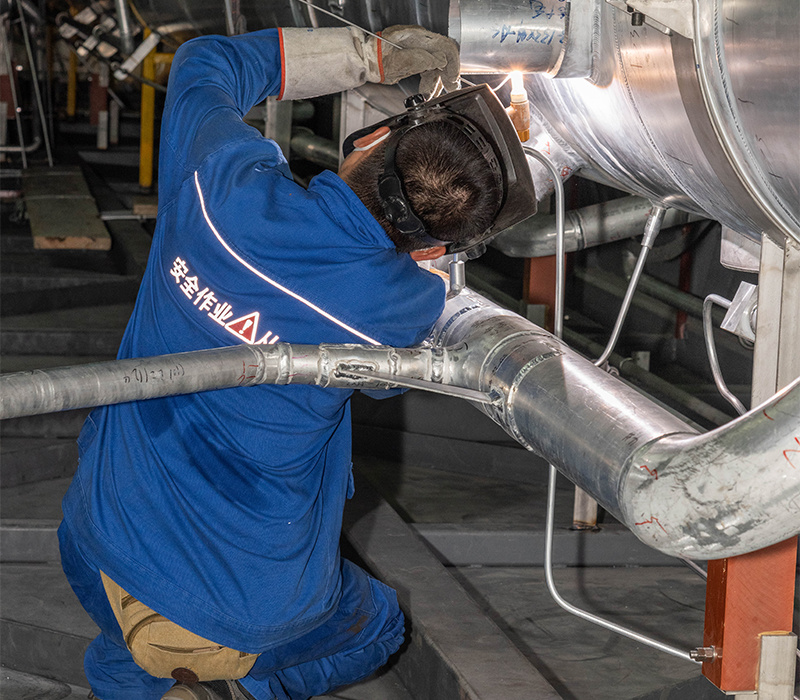
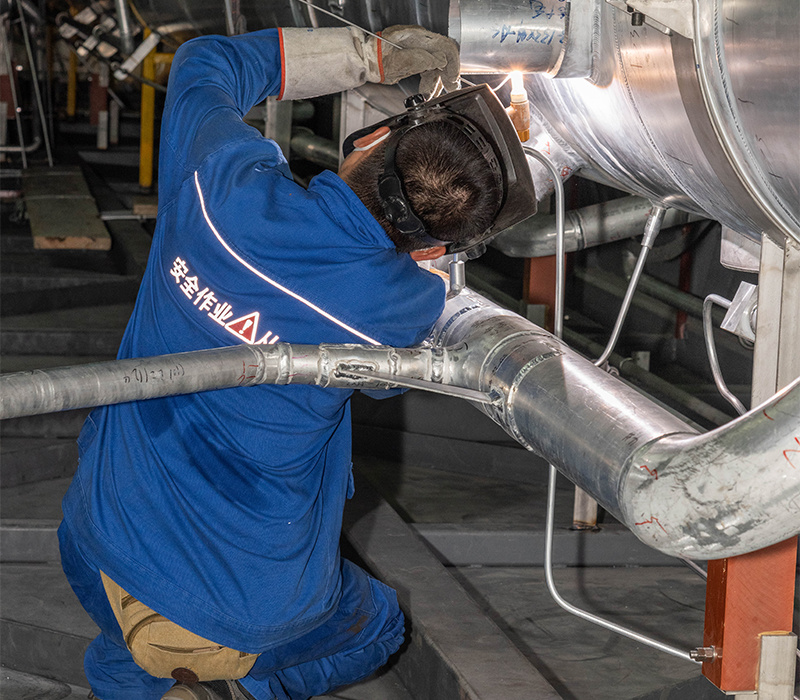
- Product Detail
-
With over 20 years of experience in research and development, design, sales, manufacturing, and the provision of complete sets of industrial gas separation, liquefaction, and industrial exhaust gas recovery and utilization systems.
• A superior working environment,
• Advanced production lines,
• Strict adherence to process specifications to ensure product quality,
• Rigorous operations in accordance with established standards,
• Fully automated CNC laser cutting machines with automatic material loading,
• A design-led approach, with collaborative design of factory models, resulting in shortened design cycles and more precise on-site assembly of prefabricated materials.
Core equipment for ASU
With over 20 years of experience in research and development, design, sales, manufacturing, and the provision of complete sets of industrial gas separation, liquefaction, and industrial exhaust gas recovery and utilization systems.
Categories:
keyword:
Core equipment for ASU
Factory
FAQ
What are the methods of air separation?
Cryogenic Distillation: This is the most common method. Air is cooled to extremely low temperatures, causing it to liquefy. The liquid air is then fractionally distilled, taking advantage of the slightly different boiling points of oxygen and nitrogen, allowing them to be separated. Adsorption: This method utilizes materials like zeolites (molecular sieves) that selectively adsorb one gas component while allowing others to pass through. By cycling the adsorption and desorption processes, pure streams of oxygen or nitrogen can be obtained. Membrane Separation: This method employs specialized membranes that allow certain gases to pass through more readily than others. Oxygen molecules tend to permeate through these membranes faster than nitrogen molecules, enabling their separation. These methods are used to produce a variety of industrial gases with diverse applications in various sectors.
What are core equipments of cryogenic distillation air separation?
Air Compressor: This component compresses atmospheric air to the necessary pressure levels to initiate the liquefaction process. Heat Exchangers: These vital components facilitate efficient heat transfer within the system. They serve to pre-cool the compressed air, recover valuable cold energy from the process streams, and maintain the requisite low temperatures throughout the system. Molecular Sieve Beds: These beds are employed to meticulously remove impurities such as water vapor and carbon dioxide from the compressed air prior to its entry into the main cryogenic section. These impurities have the potential to solidify at the extremely low temperatures encountered within the process, potentially leading to obstructions and operational disruptions. Distillation Columns: These constitute the heart of the air separation process. They incorporate trays or packing materials that effectively facilitate the separation of oxygen and nitrogen based on their inherent differences in boiling points. Expanders: These devices ingeniously convert the pressure energy inherent within the compressed air into useful work, contributing significantly to the overall refrigeration cycle and consequently reducing energy consumption.
What is oxygen extraction rate of air separation?
Oxygen Extraction Rate: The ratio of the mass of oxygen produced by the air separation unit (ASU) to the mass of oxygen present in the incoming air stream. Key Factors Influencing Oxygen Extraction Rate: ASU Design and Technology: The efficiency of the distillation columns, heat exchangers, and other components directly impacts the amount of oxygen that can be recovered. Advanced technologies like high-efficiency expanders and improved heat exchanger designs can significantly enhance extraction rates. Operating Conditions: Factors like operating pressure, temperature, and flow rates can influence the separation efficiency. Air Quality: The presence of impurities in the incoming air stream can affect the performance of the ASU and reduce oxygen extraction. Modern cryogenic air separation units typically achieve oxygen extraction rates of 95-98%.
What are the air quality requirements for an air separation unit?
Moisture Content: Low moisture levels are crucial: Water vapor can freeze within the cryogenic system, causing blockages and operational disruptions. Efficient dryers: ASUs typically incorporate drying systems, such as molecular sieve beds, to remove moisture from the incoming air. Particulate Matter: Minimizing particulates: Dust, dirt, and other particulates can damage delicate equipment like valves and bearings within the ASU. Filtration systems: High-efficiency filters are used to remove particulate matter from the incoming air stream. Hydrocarbons: Hydrocarbons can contaminate products: Hydrocarbons can condense within the cryogenic system, potentially contaminating the final oxygen and nitrogen products. Hydrocarbon removal: Catalytic converters or other methods may be used to remove hydrocarbons from the air stream. Other Contaminants: Trace gases: Depending on the location and source of the intake air, trace gases such as sulfur dioxide, nitrogen oxides, and carbon monoxide may be present. Impact on operations: These contaminants can affect the efficiency of the separation process and may require additional treatment steps. Temperature and Pressure: Consistent conditions: While not directly related to air quality, consistent ambient temperature and pressure conditions are important for optimal ASU operation. Meeting these air quality requirements is essential for the reliable and efficient operation of an ASU, ensuring the production of high-purity oxygen and nitrogen products.
Related Product